BMT Additive
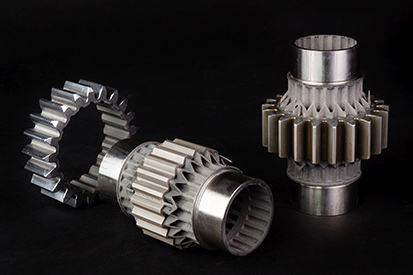
Beyond conventional metal production
TEXT: KARIN VENEMA | PHOTOS © BMT ADDITIVE
The benefits and implications of 3D metal-printing are numerous. So numerous, that many companies and designers cannot yet oversee all available options. BMT Additive sees it as their mission to help their customers discover these possibilities and use them as input for their product development. This integrated approach is crucial to ensure the maximum value of additive manufacturing.
BMT Additive is a subsidiary of the BMT Group, a longstanding giant in the field of engineering services and high-precision metal components. BMT Additive is the only company in Belgium that 3D prints titanium products for external use with Electron Beam Melting technology. They work with clients in the aerospace and transportation sector, and also co-create industrial machinery and equipment.
“Co-creation is the best method to use in the 3D field that is still growing from its infancy,” says Geert De Donder, business development manager at BMT Additive. “We offer design, printing and finishing to come up with a tailored design for functionality, the selected printing technology and finishing steps. This makes us a unique partner for our customers.”
3D metal additive manufacturing creates new possibilities in several industries. For instance, General Electric Company has recently presented the game changing Advanced Turboprop engine, which reduced 855 parts to just 12, by using additive 3D-printing technology. This means less part interfaces, leading to an improved performance. Furthermore, the engine weighs less, is more durable, and has a simplified logistic.
“At the moment, our plant is mostly research and development orientated,” says Ewald Goossens, business unit manager at BMT Additive. “We make titanium parts like brackets, valves and sprockets to the highest standards applicable in the industry sectors. At the same time, we are investigating the possibilities of aluminium, high-strength stainless steel and Inconel alloys. Industrial 3D metal printing is only just getting started, and we are at the forefront of the development.”
BMT Additive works together in several consortia to qualify for big aerospace projects. All the produced parts are subjected to stringent testing, including 100 per cent inspection. Results typically surpass clients’ expectations, due to the expert knowledge and experience available within the company.
“I sometimes call us ‘the Steve Jobs of 3D printing’,” smiles De Donder. “20 years ago, nobody imagined what the possibilities for the smartphone would be, and look at them now… The same applies to 3D printing, the possibilities are endless!”
Subscribe to Our Newsletter
Receive our monthly newsletter by email